New Rest Portugal: Trazabilidad inteligente con Andy
New Rest is a global leader in foodservice, operating in over 60 countries and managing restaurants, cafés, and catering services in airports, train stations, highways, and urban centres. With more than 40 years of experience in the industry, New Rest has become a benchmark in collective catering, serving millions of customers daily in high-traffic strategic locations.
In Portugal, New Rest manages multiple points of sale in airports and stations, where operational excellence and food safety are essential to maintaining its reputation.
The company stands out for its commitment to innovation and quality, constantly implementing new technologies to optimise operations and deliver the best dining experience in fast-paced environments.
The diversity of suppliers, high turnover of perishable goods, and strict food safety regulations created significant operational complexity.
The main obstacle was the lack of full visibility over each product’s journey from reception to final consumption. Managing expiration dates and proper stock rotation required tighter control to minimise food waste.
Responding quickly to potential health alerts and demonstrating compliance to regulatory authorities had become a strategic priority to maintain customer trust and operational continuity.
Immediate response to critical incidents
Andy’s traceability has transformed New Rest Portugal’s ability to locate any product within minutes – essential during food safety alerts to protect consumer health and minimise operational disruption.
Significant food waste reduction
Precise expiration tracking and automated stock rotation have notably reduced waste. Andy’s early alerts allow teams to plan the use of products nearing expiry, contributing to sustainability goals.
Audit process transformation
Automated reports and digital documentation have revolutionised audits. Auditors now access complete traceability records instantly, reducing preparation time and improving the accuracy of documentation.
Real-time inventory control
The elimination of manual processes has nearly eradicated inventory errors. New Rest Portugal now enjoys accurate, reliable stock control, enabling better procurement planning and supply chain optimisation.
How New Rest Portugal uses Andy
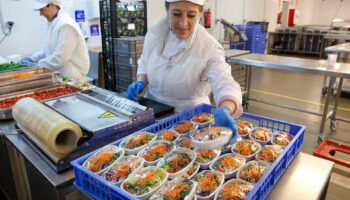
New Rest Portugal implemented Andy’s advanced labelling and traceability tools to transform its entire supply chain.
Andy’s labelling tool allows teams to automatically generate customised labels for every product, batch, and lot received.
Andy’s traceability system automatically logs every product movement – from warehouse reception to kitchen use. Employees use mobile devices to update each product’s location, status, and relevant information in real time.
This full digitisation eliminates human error and ensures complete inventory visibility.
Andy’s automatic alerts notify teams when products near their expiration date, enabling proactive stock rotation and significantly reducing waste.
The digital assistant also generates detailed traceability reports that simplify internal and external audits and demonstrate full compliance with food safety regulations.
Reed more success stories
Reed more about our partners and see how they are making real change in their business.